The heart of a modern Formula 1 car is its complex and highly efficient powertrain, and at the core of this lies the Internal Combustion Engine (ICE). Since the 2014 season, Formula 1 regulations have mandated the use of a 1.6-liter V6 turbocharged engine configuration, a significant shift from the V8 and V10 engines of previous eras.
Why V6?
The choice of a V6 configuration in Formula 1 is a result of a compromise between power, fuel efficiency, and packaging. Compared to inline engines, V-engines are more compact, especially in width, which is crucial for aerodynamic packaging and car design in F1. A V6 offers a good balance:
- Compactness: Shorter and narrower than inline-6 engines, fitting neatly within the aerodynamic constraints of an F1 car.
- Power Delivery: V6 engines can be designed to produce significant power, especially when turbocharged. The 1.6-liter V6 engines in F1 are capable of generating over 700 horsepower on their own, and even more when combined with the hybrid system.
- Fuel Efficiency: Regulations emphasizing fuel efficiency pushed F1 towards smaller displacement engines. The V6 configuration, combined with turbocharging and hybrid systems, allows for high power output while adhering to strict fuel consumption limits.
- Vibration and Balance: V6 engines, particularly those with a 60-degree or 90-degree bank angle, can be inherently well-balanced, reducing vibrations and improving engine longevity and performance.
Cylinder Bank Angle
The "V" in V6 refers to the configuration where the cylinders are arranged in two banks, set at an angle to each other, forming a "V" shape. The cylinder bank angle is a critical design parameter that influences engine balance, width, height, and overall performance. Common V6 engine bank angles include 60°, 90°, and sometimes 120°.
-
60-degree V6: This is often considered the ideal V6 configuration for balance. A 60-degree V6 can be inherently balanced, meaning it can operate smoothly without requiring balance shafts. This configuration minimizes vibration, enhancing engine reliability and driver comfort. It also tends to be narrower and shorter than other V6 configurations.
-
90-degree V6: While not inherently balanced in its primary configuration, a 90-degree V6 is easier to design from a manufacturing perspective, especially if manufacturers are adapting from V8 engine production lines (where 90 degrees is a common angle). To mitigate imbalance, 90-degree V6 engines often employ balance shafts. A 90-degree V6 can be wider than a 60-degree V6 but may be shorter in height.
-
Cylinder Bank Angle in F1: Formula 1 engine manufacturers have predominantly favored wider V-angles, likely closer to 90 degrees or greater, in their 1.6L V6 turbo hybrid engines. While specific bank angles are closely guarded secrets, the wider angle helps in lowering the engine's center of gravity, which is beneficial for handling. A wider angle also potentially aids in packaging ancillaries within the tight confines of an F1 car and can offer advantages in terms of crankshaft and exhaust manifold design.
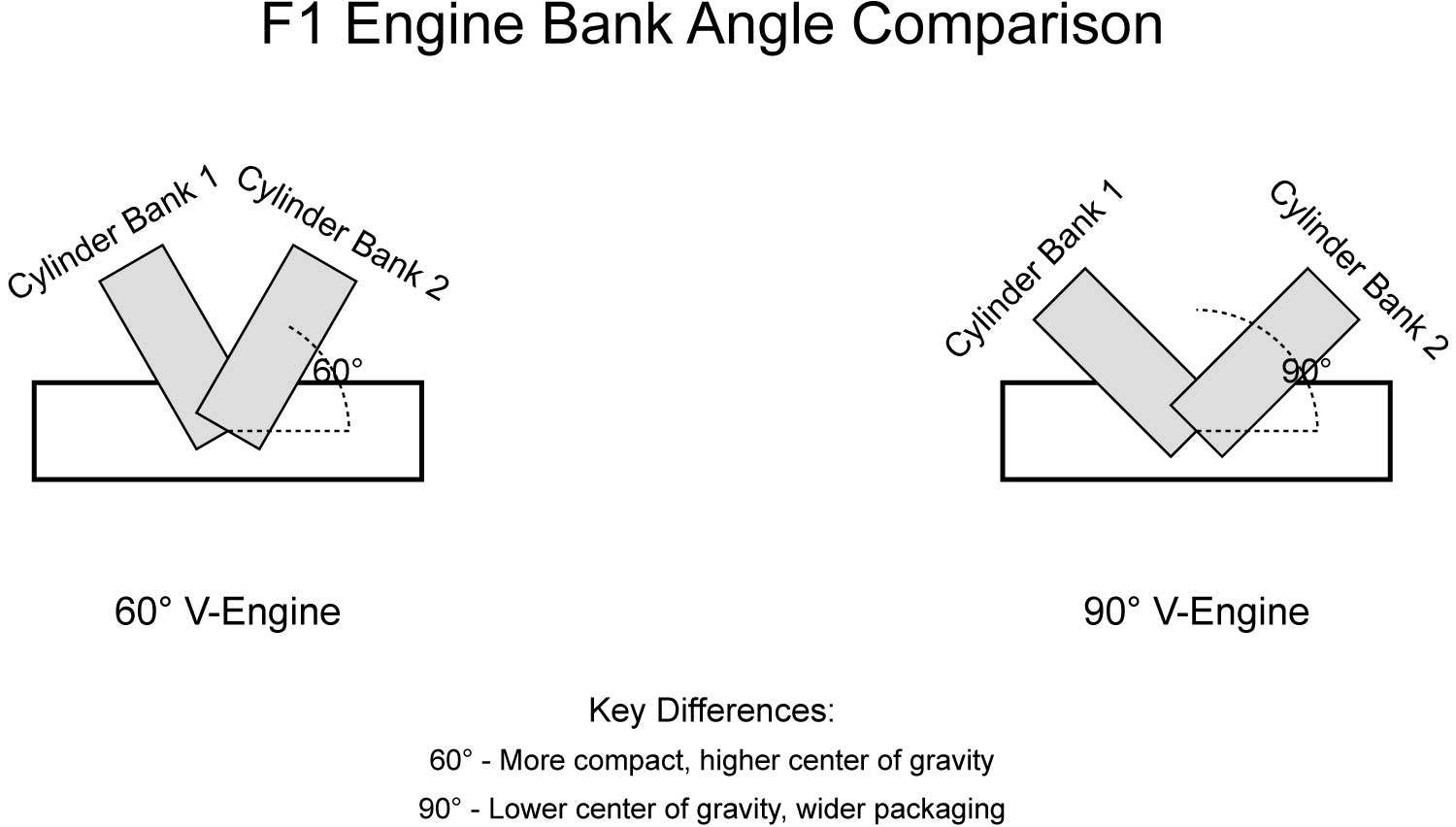
Materials: Pushing the Boundaries of Engineering
Formula 1 engines operate under extreme conditions, enduring immense temperatures, pressures, and stresses. To withstand these conditions and deliver maximum performance, F1 engine components are crafted from advanced materials:
-
Engine Block and Cylinder Head:
- High-Strength Aluminum Alloys: Typically, aluminum alloys are used for the engine block and cylinder heads to minimize weight while providing necessary strength and thermal conductivity. These are not just standard aluminum but highly specialized alloys containing elements like silicon, copper, magnesium, and others, tailored for specific properties like high-temperature strength and wear resistance.
- Steel Liners or Coatings: Cylinder bores within the aluminum block may feature steel liners or advanced coatings (like Nikasil or Plasma Spray coatings) to enhance wear resistance and durability, as aluminum alone is too soft to withstand piston friction over extended periods.
-
Pistons and Connecting Rods:
- Forged Aluminum Alloys or Titanium: Pistons are often made from lightweight forged aluminum alloys to reduce reciprocating mass, allowing for higher engine speeds and quicker response. In some high-stress applications, or for connecting rods, titanium alloys might be used for their exceptional strength-to-weight ratio, despite being more expensive and challenging to manufacture.
-
Crankshaft:
- High-Strength Steel Alloys: The crankshaft, bearing the brunt of combustion forces and rotational stress, is made from very high-strength steel alloys, often forged and then meticulously machined and balanced. These alloys are chosen for their fatigue resistance and ability to maintain dimensional stability under extreme loads and temperatures.
-
Valves and Valve Springs:
- Titanium Valves: To enable very high engine speeds, valves are often made from titanium alloys. Titanium's low density reduces inertial mass, allowing for faster valve operation and reduced risk of valve float at high RPMs.
- High-Performance Steel Alloys for Valve Springs: Valve springs need to endure millions of cycles under high stress and temperature. They are manufactured from specialized high-performance steel alloys designed for fatigue resistance and consistent spring rates at elevated temperatures. Pneumatic valve springs, using compressed air, are also employed in F1 engines to manage valve control at extremely high RPMs.
-
Turbocharger Components:
- Nickel-based Superalloys (Inconel): The turbine in the turbocharger operates in extremely high temperatures from the exhaust gases. Materials like Inconel, a family of nickel-based superalloys, are used for turbine blades and housings due to their exceptional high-temperature strength, creep resistance, and oxidation resistance.
-
Exhaust System:
- Titanium and Inconel: Exhaust manifolds and exhaust systems in F1 also experience very high temperatures and thermal stress. Materials like titanium and Inconel are used for their heat resistance, strength, and also for weight reduction, especially in the hot exhaust sections.
-
Fasteners and Seals:
- High-Tensile Steel and Specialized Alloys: Even seemingly minor components like fasteners (bolts, studs) and seals are made from high-specification materials to ensure reliability under extreme conditions. High-tensile steels and specialized polymers or elastomers capable of withstanding high temperatures and aggressive fluids are used.
Manufacturing Precision
Beyond the choice of materials, the manufacturing processes for F1 engine components are incredibly precise. Tolerances are measured in microns, and components undergo rigorous testing and quality control. Techniques like CNC machining, Electrical discharge machining (EDM), precision casting, and advanced welding are employed to create engine parts that are both incredibly strong and lightweight.
The V6 engine architecture in Formula 1 represents a pinnacle of engineering, balancing power, efficiency, and packaging within stringent regulations. The cylinder bank angle and the selection of exotic materials are crucial elements in achieving the performance and reliability demanded in the world's most technologically advanced motorsport. The relentless pursuit of performance pushes engineers to constantly innovate with materials and design, ensuring that the F1 engine remains a marvel of modern engineering.